Preventing Weld Undercut Made Easy: Secret Techniques Unveiled
Preventing Weld Undercut Made Easy: Secret Techniques Unveiled
Blog Article
Grasping the Art of Welding: Just How to Stay Clear Of Undercut Welding Issues for Flawless Fabrication Results
Performance and accuracy are extremely important in the world of welding, where even the tiniest blemish can endanger the architectural integrity of a produced piece. One typical difficulty that welders face is undercutting, a problem that can deteriorate a weld joint and lead to expensive rework. By understanding the origin of undercut welding and applying reliable strategies to stop it, welders can raise their craft to new levels of excellence (Preventing weld undercut). In the search of perfect construction results, mastering the art of welding to avoid undercut problems is not just a skill but a need for those pursuing perfection in their job.
Comprehending Undercut Welding

To avoid undercut welding, welders should make sure proper welding criteria, such as readjusting the existing, voltage, traveling rate, and keeping the right electrode angle. Additionally, making use of the suitable welding method for the particular joint arrangement is necessary. Employing weaving movements or backstepping methods can assist make certain correct weld steel deposition and decrease the chance of undercut formation. Normal inspection of welds during and after the welding procedure is likewise crucial to catch any type of undercut very early and make necessary changes to avoid more issues. Preventing weld undercut. By understanding the sources of undercut welding and executing preventative measures, welders can achieve top notch, structurally audio welds.
Reasons For Undercut in Welding
Comprehending the variables that add to undercut in welding is necessary for welders to generate premium, structurally audio welds. Inadequate welding incorrect or present welding speed can also add to damage. Recognizing these reasons and implementing correct welding techniques can help avoid damaging problems, making certain strong and long lasting welds.
Techniques to avoid Undercutting

To mitigate the threat of damaging in welding, welders can use critical welding methods aimed at boosting the high quality and stability of the weld joints. Furthermore, using the correct welding strategy for the particular joint configuration, such as weave or stringer beads, can contribute to minimizing undercutting.
Furthermore, correct joint prep work, including making certain clean base products devoid of impurities and utilizing the appropriate welding consumables, is critical in avoiding undercut issues. Using back-step welding methods and controlling the weld bead account can likewise help disperse heat uniformly and minimize the danger of undercut. Regular examination of the weld joint during and after welding, along with implementing high quality guarantee actions, can aid in attending to and identifying damaging issues quickly. By applying these techniques vigilantly, welders can accomplish remarkable manufacture results with marginal undercut defects.
Value of Correct Welding Parameters
Choosing and maintaining suitable welding parameters is important for attaining effective welds with very little flaws. Welding specifications refer to variables such as voltage, present, take a trip speed, electrode angle, and shielding gas circulation rate that directly impact the welding process. These criteria need to be very carefully adjusted based upon the sort of material being welded, its density, and the welding technique used.
Appropriate welding specifications guarantee the correct amount of heat is used to melt the base metals and filler material uniformly. If the criteria are established too expensive, it can bring about extreme warmth input, triggering distortion, spatter, or burn-through. On the other hand, if the specifications are too low, incomplete blend, absence of infiltration, or damaging might take place.
Quality Control in Welding Procedures
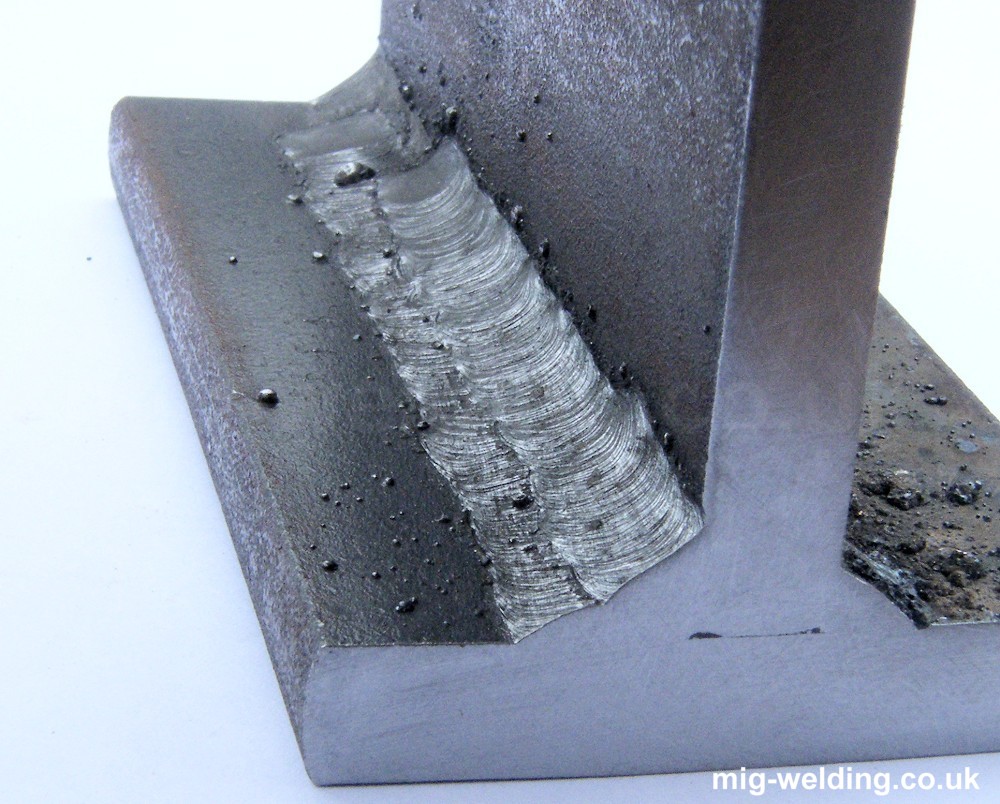
Conclusion
To conclude, mastering the art of welding calls for an extensive understanding of undercut welding, its causes, and methods to avoid it. By guaranteeing correct welding criteria and carrying out quality control practices, remarkable fabrication outcomes can be accomplished. It is important for welders to constantly pursue excellence in their welding procedures to stay clear of undercut helpful site concerns and create top quality welds.
Undercut welding, a common flaw in welding procedures, happens when the weld metal does not correctly fill the groove and leaves a groove or clinical depression along the bonded joint.To stop undercut welding, welders ought to make certain appropriate welding parameters, such as changing the present, voltage, travel rate, and maintaining the proper electrode angle. Inadequate welding incorrect or existing welding speed can likewise add to undercut.To mitigate the danger of undercutting in welding, welders can utilize strategic welding methods intended at enhancing the quality and integrity of the weld joints.In Visit This Link final thought, understanding the art of welding requires a thorough understanding of undercut welding, its reasons, and techniques helpful resources to avoid it.
Report this page